Technologies & Applications > Servo Control
Servo Control
How Servo control combines power and precision
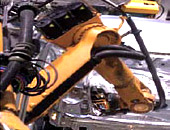
Servo drive systems are increasingly being used in place of a standard AC motor as they offer superior control. Characteristics such as a high power output to physical size ratio and fast acceleration, making them ideal for many applications. These include packaging, product handling, printing and other industrial machinery where precision is critical.
In general, the application of a servo motor is characterised by the requirement for frequent changes in speed and torque, operation from standstill to hold positions and short-term operation with high peak loads. The common form of industrial servo system uses an AC brushless synchronous motor with an integral absolute encoder to provide feedback. In comparison to standard threephase AC motors, servo motors are considerably more compact with a higher power density, higher efficiency and significantly lower inertia. Hence they accelerate much faster, run cooler, and provide instant power for automation tasks.
Servo Control System
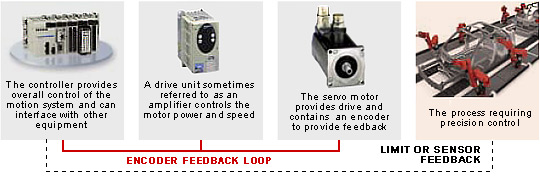
The drive unit handles power and speed control of the servo motor. In contrast to three-phase AC motors without speed feedback, the servo motor not only has power terminals and an earth connection, but also connections for the integral shaft encoder. In some cases it will also have brake control and temperature monitoring connections. The encoder feedback loop is key to the entire system and continually provides motor output shaft speed and position data. This allows the drive unit to compensate for changes in load conditions, which will affect the shaft speed and monitor the exact position of the shaft. This enables the system to drive the motor to a precise position. The controller, which could be a PLC or dedicated motion controller, provides overall control of the system. This controller provides commands to the drive unit as either simple ‘move’ parameters via a fieldbus interface (for example Modbus, or CANopen) or using pulse and direction signals. The controller also monitors sensors and limit inputs to ensure the process is completed correctly and doesn’t exceed predefined limits.
Junma Servo Series
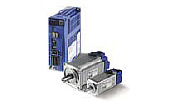
The Junma range offer the user a compact servo drive and motor combination which is simple to use, as the product has no parameters to set and features an automatic tuning system. Pulses from a suitable controller are sent to the drive, along with direction control. The servo drives are available in 100, 200, 400 and 750W models, with matching motors.